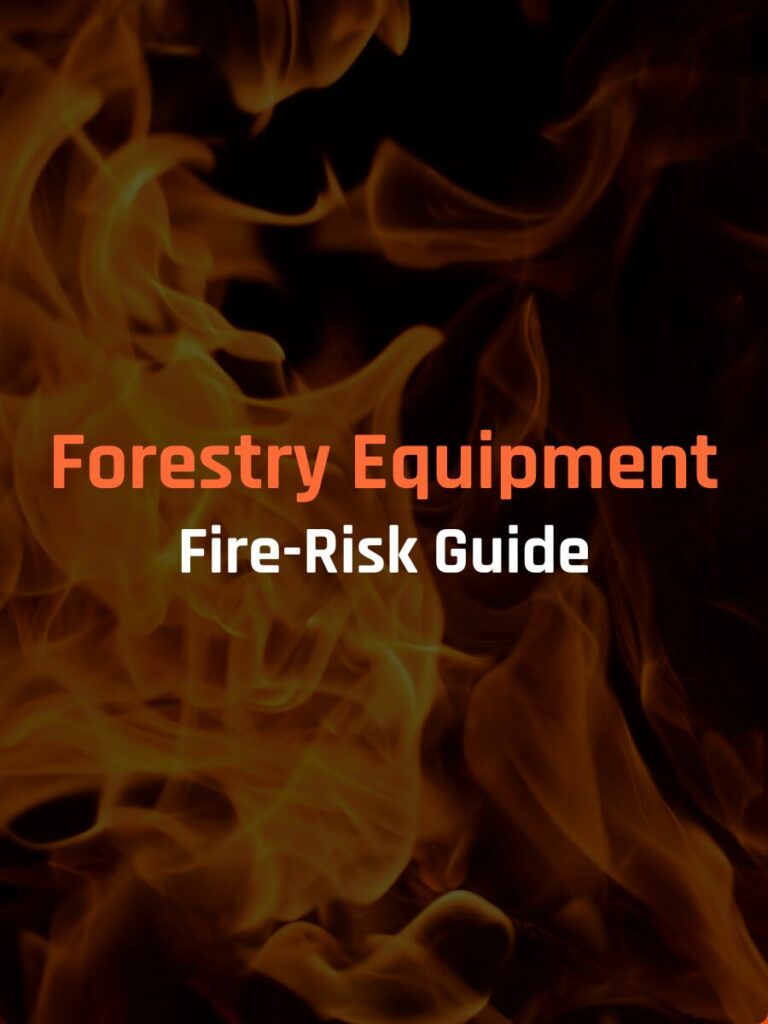
Choosing the right automatic lubrication system (ALS) is a crucial step in optimizing the performance and lifespan of your machinery. Whether you operate in the construction, manufacturing, or transportation sectors, automatic lubrication ensures your equipment runs efficiently by minimizing wear and tear. This guide will walk you through the key factors to consider when selecting an ALS for your specific needs.
In industries where heavy machinery is part of everyday operations, the risk of fire is something that can’t be ignored. Whether you’re in construction, mining, or another industrial sector, fire hazards are real. Fire suppression systems are designed to detect fires early and respond quickly—often before you even realize there’s a problem—helping to prevent significant damage.
Different types of machinery require different lubrication solutions. It’s important to identify which components need lubrication and the operating conditions under which your equipment functions. Consider factors like:
For example, systems that operate in extreme temperatures, like those used in mining or agriculture, may need lubricants specifically formulated for high or low-temperature environments. Suppliers like Graco, SKF Lincoln, and Bijur Delimon offer robust solutions designed to handle a variety of challenging environments.
Before investing in an ALS, it’s important to decide whether your operations would benefit more from automatic or manual lubrication. Manual lubrication can be time-consuming and prone to human error. In contrast, an automatic lubrication system offers:
Switching from manual to automatic lubrication is especially beneficial for equipment in industries like construction or fleet management, where downtime translates into significant revenue loss. Brands like SKF Lincoln and Graco offer highly reliable solutions that can be tailored to specific equipment needs.
There are different types of ALS designed for various applications, and choosing the right one depends on your machinery and operational needs. Some common types include:
When choosing an ALS, consider the ease of installation and the level of ongoing support you’ll need. Choosing a partner who offers full service—from system design to installation and maintenance—is critical to ensuring your lubrication system runs smoothly. At GreasePoint, we offer:
While automatic lubrication systems are an investment, they save you money in the long run by reducing downtime, maintenance costs, and equipment failures. Consider the following:
To help you calculate the return on investment, we offer an ROI calculator to see how much an automatic lubrication system could save your business over time.
Modern ALS come with remote monitoring capabilities, such as the GreaseAlert monitoring system offered by GreasePoint. These systems provide real-time data on lubrication levels, potential faults, and overall system health, helping operators catch issues before they become costly problems. Key benefits include:
Investing in a system with these capabilities can greatly improve your operational efficiency and minimize unexpected breakdowns.
Choosing the right automatic lubrication system is about understanding your equipment’s needs, balancing cost with operational efficiency, and ensuring you have the right support in place for system installation and maintenance. With the right ALS, you’ll be able to increase productivity, reduce downtime, and extend the life of your equipment.
At GreasePoint, we specialize in designing and installing automatic lubrication systems tailored to your industry’s specific needs. Partnering with industry leaders like Graco, SKF Lincoln, and Bijur Delimon, we provide the highest quality systems and support. Contact us today to find out how we can help optimize your equipment’s performance and keep your operations running smoothly.
We’re looking forward to working with you. Whether you have questions about products or services, our team is ready to help.