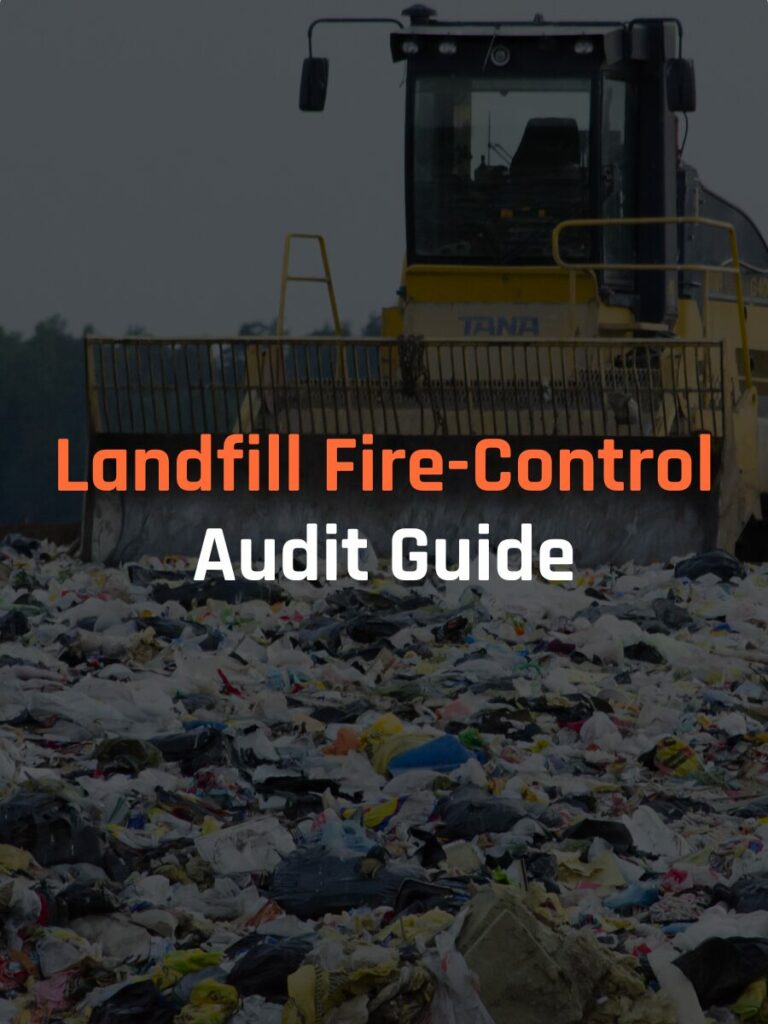
When it comes to maintaining heavy equipment, selecting the right lubrication system is crucial for ensuring efficiency, reducing downtime, and extending the lifespan of your machinery. With various options on the market, it can be challenging to identify which system best suits your needs. This guide breaks down the most popular lubrication systems, their features, benefits, and ideal applications to help you make an informed decision.
Automatic lubrication systems (ALS) provide consistent, precise lubrication to machinery components, reducing wear and tear. Unlike manual lubrication, ALS minimizes human error, saves time, and optimizes equipment performance.
At GreasePoint, we understand choosing the right lubrication system is key to maintaining your equipment’s productivity and efficiency. Our experts are here to guide you through the decision-making process, ensuring you find the best solution tailored to your industry.
We’re looking forward to working with you. Whether you have questions about products or services, our team is ready to help.